Our Products
-
ALLOYS PRODUCTS
- Stainless Steels
- Duplex And Super Duplex Steel
- Nickel Alloys
- Titanium Alloys OUR PRODUCTS
- Coils
- Sheets & Plates
- Round Bars
- Pipes & Tubes
- Scrap
- Pure Nickel Strips & Busbars
Stainless Steels
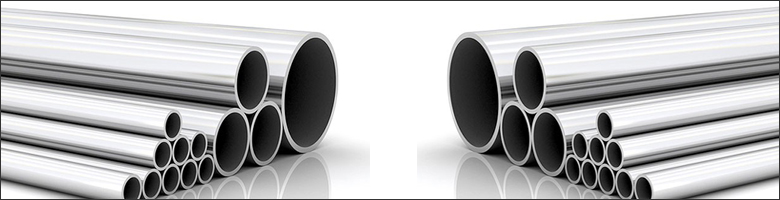
Stainless steel is a steel alloy that must contain a minimum of 10.5% chromium and contains levels of nickel, molybdenum, and niobium.
Compared to regular steel, stainless steel does not easily corrode, stain, or oxidize/rust. Stainless steel is available from Calico Metal Industries in a extensive range of forms, grades, finishes, gauges, widths, and lengths. Many different industries rely on stainless steel for a wide range of applications including aerospace, automotive, manufacturing, oil and gas, and many more. If you cannot find the exact type of stainless steel you are looking for, please call or contact us.
Stainless Steel Grades
Type 304
The most common grade; the classic 18/8 stainless steel. Also referred to as "A2" in accordance with International Organization for Standardization ISO 3506.
Type 310S
Type 310S is a low carbon austenitic stainless steel. Known for its ability to withstand high temperature applications, Type 310S, which is a lower carbon version of Type 310, also offers users an array of benefits including:
● Outstanding corrosion resistance
● Good aqueous corrosion resistance
● Not prone to thermal fatigue and cyclic heating
● Superior to Type 304 and 309 in most environments
● Good strength in temperatures up to 2100°F
Type 316L
The second most common grade (after 304); for food and surgical stainless steel uses; Alloy addition of molybdenum prevents specific forms of corrosion. Also known as "marine grade" stainless steel due to its increased resistance to chloride corrosion compared to type 304. SS316 is often used for building nuclear reprocessing plants. Most watches that are made of stainless steel are made of this grade. Rolex is an exception in that they use Type 904L. 18/10 stainless often corresponds to this grade. Also referred to as "A4" in accordance with International Organization for Standardization ISO 3506.
Type 321
Similar to 304 but lower risk of weld decay due to addition of titanium. See also 347 with addition of niobium for desensitization during welding.
● Good forming and welding
● Works well up to about 900°C
● Not for decorative uses
Type 321H
Type 321H, is a titanium stabilized austenitic stainless steel that is known for its general corrosion resistance. This higher carbon version of Type 321 stainless steel offers a wide variety of benefits including
● Excellent resistance oxidation to 1500°F (816°C)
● Good low temperature toughness
● Comparable corrosion resistance and machinability to Type 304
● Readily welded by most standard processes
● Very ductile and forms easily
Type 904L
Type 904L is a high alloy austenitic stainless steel that is known for its corrosion properties. This low carbon version of Type 904 stainless steel also offers other benefits to users including
SMO 254
Alloy 254, which is also found under the brand name Sandvik 254 SMO and UNS S31254, is a super austenitic stainless steel that is well known for its outstanding resistance to pitting, crevice corrosion, stress cracking, and fatigue corrosion. One reason for these unique properties is Alloy 254’s specific chemical make-up that includes
● Fe (remainder)
● Cr 19.5-20.5%
● Ni 17.5-18.5%
● Mo 6-6.5%
● Mn 1.0% max
● Si 0.8% max
● P 0.03% max
● C 0.02% max
Alloy 20
Specifically designed to withstand sulfuric acid Alloy 20 offers excellent corrosion resistance. Due to its nickel, chromium, molybdenum and copper levels Alloy 20 is ideal for use in corrosive environments. At 33% nickel, Alloy 20 has practical immunity to chloride stress corrosion cracking. This alloy is often chosen to solve stress corrosion cracking problems, which may occur with 316L stainless.
● Sulfuric acid pickling tanks, racks and heating coils
● Phosphate coating drums and racks
● Heat exchangers
● Bubble caps
● Process piping
● Mixing tanks
● Chemical and petroleum process equipment
Type 430
Decorative, e.g., for automotive trim; ferritic. Good formability, but with reduced temperature and corrosion resistance.
Type 17-4 PH
17-4 PH, also known as UNS S17400, is a martensitic precipitation-hardening stainless steel. 17-4 PH is popular with our customers due to its excellent combination of good corrosion resistance and high strength. In order to be considered 17-4 PH, an alloy must be made of a unique set of chemical elements:
● Fe Balance
● Cr 15-17%
● Ni 3-5%
● Cu 3-5%
● Mn 1.5% max
● Si 0.7% max
● Nb 0.45% max
Type 15-5 PH
15-5 PH, also known as also known as UNS S15500 or XM-12,is a martensitic, precipitation hardening stainless steel. Popular due to its high strength and good corrosion resistance, 15-5 PH also offers user a host of other benefits:
● Good mechanical properties at temperatures up to 600°F (316°C)
● Excellent longitudinal and transverse toughness
● Good in corrosive and high-pressure environments
● Equivalent weldability to 17-4 PH with greater toughness
● Low temperature hardening
A-286
If you need a stainless steel which offers superior strength upto temperatures of 537.77C and excellent oxidation resistance in temperatures upto 815.55C then look no further than NeoNickels A-286 Stainless Steel. Now available in a variety of product forms.
● Jet engine components
● High temperature fasteners, springs
● Non-magnetic cryogenic equipment
AL-6XN
With over 25 years of proven seawater service and 50% stronger than stainless steel, AL-6XN® is the material of choice for many applications and industries around the world.
● FGD Scrubbers
● Reverse Osmosis
● Distillation Columns
● Heat Exchangers